在正常情況下,該混凝土以柱體的形式進行流動,該柱體形成在管泵送流體流動的懸浮液中心。其表面涂有一層流體灌漿,灌漿層被作為其與管壁之間接觸的潤滑劑,在混凝土的運輸過程中骨料與骨料之間基本是不發生接觸的。當在某些骨料運動過程中粗骨料的運動受阻,就會導致骨料背后骨料的聚集,由于沖擊速度逐漸停滯,造成粗骨料管壁上支撐粗骨料的砂漿被排擠,而留下的間隙又會被細骨料所填補進來,從而導致了骨料的密度增加。管道中的散裝物料沿管道的徑向膨脹,導致水泥漿潤滑層被破壞,管道中的混凝土運動阻力變大,使得運動速度不斷降低甚至停止,一旦運動停止就會導致堵塞,從而形成堵管。
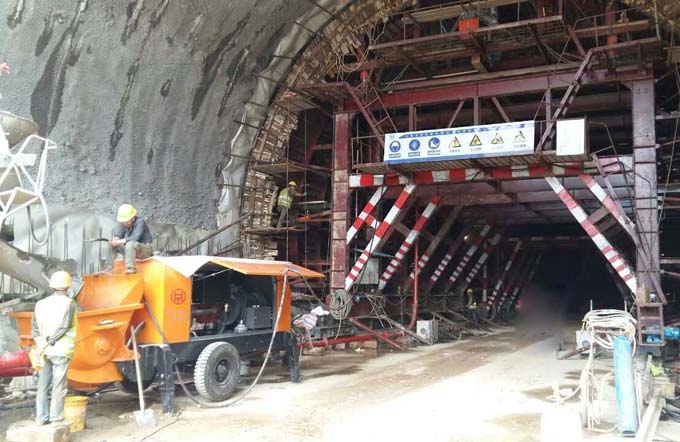
1、混凝土傳輸過程中操作上的錯誤
(1)由于造作人員在操作過程中的粗心大意導致的問題。在進行混凝土泵送的過程中,相關的操作人員應當時刻留意壓力表的顯示數據,一旦發現泵送壓力表的示數過大就應當立刻采取相應的措施。具體操作應該先進行反泵輸送,如此進行2~3個行程以后再正向進行泵送,這樣一般都能夠解決堵管的問題。如果在進行以上操作以后還是無法解決問題,這時候就應當立刻停止泵送,進行拆管清洗,以避免其進一步堵塞。
(2)對于泵送的速度選取不當。在進行混凝土的泵送時對于速度的選取極為重要,選取時不能夠僅僅為了加快泵送的速度而選取過大的速度,這樣的話反而會造成一些故障,嚴重影響泵送的速度。在第一次進行泵送的時候,由于管壁并沒有任何潤滑,導致其在輸送過程中的阻力較大,這時應當選取較低的速度進行輸送,等到能夠正常的泵送以后再逐漸的提高泵送的速度。如果在泵送的過程中發現混凝土塌落度過低或者發現其存在堵管的傾向是應當立刻降低輸送的速度,以避免其發生堵管。
(3)對于泵送余料量的控制不夠到位。在進行泵送的過程中一定要控制好余料的量,如果余料的量過多,超過了防護欄,那么在進行粗骨料的清理時便會造成不方便;如果余料的量過少,一旦其低于攪拌軸,那么在輸送的過程中很容易吸入空氣,而一旦在管道中吸入空氣便容易導致堵管。
(4)停歇時間過長。在一般的泵送過程中,停機的時間并不是固定的,需要根據當地的具體溫度、混凝土初凝時間以及塌落度來確定的,一般而言在5~10min便需要開泵一次。如果停機的時間過長么那么很容易導致管道內混凝土的凝結,這時便不能夠在繼續進行泵送了。
(5)對于管道的清潔不夠到位。在上次的管道使用以后沒有做好相應的清潔工作,導致了管道的內壁還存在一些殘留的混凝土,這很容易導致管道的堵塞。因而在每一次的泵送以后都需要做好管道的清理工作,確保管道被清洗干凈。
2、管道連接原因導致的堵管
在管道連接的過程中一定要遵從相應的連接方法,如果管道連接錯了那么便會容易產生堵管。連接管道時具體需要遵守以下幾個原則:
(1)在進行管道的布置時應當確保布置的管道最短,對于管道的彎頭應當盡量少的布置,如果無法避免彎頭那么也應當盡量布置彎角較大的彎頭,從而最大程度上降低管道阻力,降低堵管的可能性。
(2)在泵的出口椎管處不能夠直接接上彎管,如果一定要接彎管的話必須要先接上5mm以上的直管以后才能夠再接上彎管。
(3)如果在傳輸過程中需要在中間加設管道,每次最多智能接一根,并且在進行接管時必須要先對于管道內壁進行潤滑,然后排凈管道內的空氣,從而避免其引發堵管。
(4)在垂直向下傳輸的管道段應當在其出口處加設防離析裝置,避免管道堵塞。
3、混凝土或砂漿的離析導致的堵管
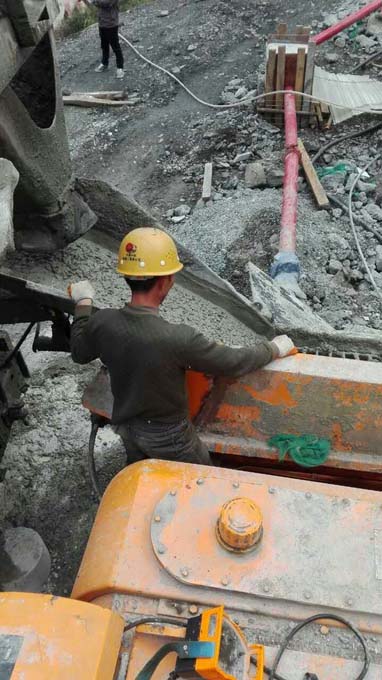
當混凝土或砂漿遇水時,極易造成離析。有時候進行泵送砂漿時,會發生堵塞的現象,是因為砂漿和水在管道中發生接觸從而引發砂漿的離析造成的,預防方法是:在進行泵送之前先用水浸濕管道,然后從管道的最低點出將管道的連接松開,將管道內的水全部排盡。在完成混凝土的泵送以后清洗管道時應當在管道內加入海綿球,從而將水域混凝土隔離開來,從而避免造成堵管。
4、局部漏漿造成的堵管
在混凝土傳輸的過程中,如果發生漏漿,一方面會對于混凝土的質量造成影響,另一方面也會導致管道內部壓力降低,混凝土的塌落度降低,從而容易導致堵管。而在混凝土傳輸過程中產生漏漿的主要原因有以下幾種:
(1)在進行管道的連接時沒有能夠做好管道的連接,從而在混凝土的泵送過程中接頭處發生松動、損壞,從而導致漏漿。對此應當及時對于接頭處進行加固,并且更換密封圈。
(2)混凝土輸送缸嚴重磨損。在混凝土輸送過程中有時候會發現水箱中的水很快變得渾濁不清,檢測后發現輸送缸磨損嚴重,此時應當及時將嚴重磨損的輸送缸更換掉。
(3)混凝土活塞嚴重磨損。混凝土傳輸過程中如果發現水箱中水變得渾濁或者在水箱中發現存在砂漿,那么很大可能是因為混凝土活塞已經被嚴重的磨損了。對此應當及時的將嚴重磨損的活塞更換掉,否則將會導致堵管。
5、混凝土塌落度的控制不合理
混凝土塌落度的大小直接反映了混凝土流動性的好壞,混凝土的輸送阻力隨著塌落度的增加而減小。泵送混凝土的塌落度一般在8~18cm范圍內,對于長距離和大高度的泵送一般需嚴格控制在15cm左右。塌落度過小,會增大輸送壓力,加劇設備磨損,并導致堵管。塌落度過大,高壓下混凝土易離析而造成堵管。
6、水泥用量不合理
水泥在泵送混凝土中,起膠結作用和潤滑作用,同時水泥具有良好的保水性能,使混凝土在泵送過程中不易泌水,水泥的用量也存在一個最佳值,若水泥用量過少,將嚴重影響混凝土的吸入性能,同時使泵送阻力增加,混凝土的保水性變差,容易泌水、離析和發生堵管。一般情況下每立方米混凝土中水泥含量最低不能少于300kg,但也不能過多,水泥用量過多,將會增加混凝土的粘性,從而造成輸送阻力的增加。另外水泥用量與骨料的形狀也有關系,骨料的表面積越大,需要包裹的水泥漿也應該越多,相應地水泥的含量就越大。因此,合理地確定水泥的用量,對提高混凝土的可泵性,預防堵管也很重要。
7、外加劑的選用不合理
混凝土在傳輸的過程中必然會需要添加一些外加劑,外加劑的種類很多,包括:超塑化劑、泵送劑、加氣劑、緩凝劑以及減水劑等,傳輸的混凝土種類不同所需要添加的外加劑也不同。外加劑的添加對于混凝土的傳輸極為重要,如果外加劑的添加不正確就會導致混凝土的流動性降低,并且導致其可泵性變差,在泵送過程中容易發生堵管。
8、氣溫變化導致的堵管
在混凝土的傳輸過程中,溫度對于其正常的傳輸有著極大的影響。在夏季時,在太陽的照射下技藝導致混凝土脫水,從而導致管道的堵塞。而在冬季時由于溫度過低很容易導致混凝土的凝結。因而在泵送過程中一定要做好管道的溫度控制,在夏季時注意做好管道的降溫工作,而在冬季則應當做好管道的保溫工作。
堵管位置的判斷及排除方法
1、進料口處的堵塞
現象:在傳輸的過程中發現泵送系統各部分均正常工作,并不存在任何故障,在料斗中發現了較大的骨料以及結塊,在料口處進料被卡住了。
解決方法:進行反向泵送,從而由內部破壞結塊,在混凝土回到料斗中以后進行攪拌,待其攪拌完成以后再進行泵送。如果在進行以上操作以后任然不存在作用,那么就需要進行人工清理了。
2、分配閥出料口處的堵塞現象
現象:泵送系統不在運作,其中伴有一些雜音,設備發生劇烈的振動,而管道中不存在振動。
解決方法:首先向料斗中注入25L左右的水泥,然后反復進行正、反泵送,從而打通管道。如果在進行以上操作以后任然不存在作用,那么就需要進行人工清理了,人工將管道拆除然后清除其內部的雜物。
3、混凝土輸送管道堵塞
現象:管道內輸送壓力上升,料斗的料位不變,并且在出料口不出料。泵發生劇烈的振動,而管道也在不同的振動。
對于堵塞部位的判斷:一般而言管道的堵塞均位于轉交處,對此可以用小錘進行敲打來判斷具體的堵塞位置,在敲打的過程中如果管道的聲音較為清脆說明并沒有發生堵塞,如果較為沉悶說明該處發生了堵塞;也可以用耳朵直接進行聽聲音來判斷,如果通道的聲音為沙沙的聲音說明其傳輸正常,而如果其伴有雜聲,說明該處多半已經堵塞。
解決方法:對于管道的堵塞一般都是采用管道的正反泵送來打通管道的,期間也可以用小錘對于管道加以敲擊來促進管道的疏通。如果以上防范無效那么久需要對于管道的堵塞位置進行查明,然后將管道拆卸開來,以高壓水槍進行沖洗,確保其沖洗干凈以后再接好管道繼續泵送。
預防措施及解決方法
(1)在進行管道的安裝時盡量避免轉角,尤其應當避免S行的轉角以及90°轉角,從而最大程度上降低管道的內部阻力,避免管道的堵塞。
(2)在進行泵送作業時應當保證中間停機時間不能夠超過限制標準,避免因為停機時間過長導致其內部混凝土的凝結從而引發管道的堵塞。如果必須要進行長時間停機,那么應當5~10min作業進行一次泵的正反轉,以避免管道的堵塞。
(3)對于骨料的選擇一定要合理。粗骨料的直接不能夠大于管道直接的1/4。
(4)在進行混凝土的泵送之前要現對于管道進行潤滑,然后進行砂漿的舒適,最后才能夠進行混凝土的泵送。
(5)在夏季進行泵送是需要做好管道的降溫措施,避免因為溫度過高從而導致混凝土塌落,管道堵塞。
(6)在陡坡向下坡布置管路時,到一定的管路下端布置一緩沖水平段或管口朝上的傾斜坡段,以減少混凝土自落產生離析而堵塞,但具體位置按坡度和坡長而確定。
我這里表述的只是一部分。通過以上的說明希望會幫助到更多同行的朋友們,當然如有更好的方法或建議我們歡迎各位新老朋友加我QQ:2329242728進行交流。
友好合作熱線:0731-85053168 85053918 13873110831 朱總
郵 箱:[email protected]